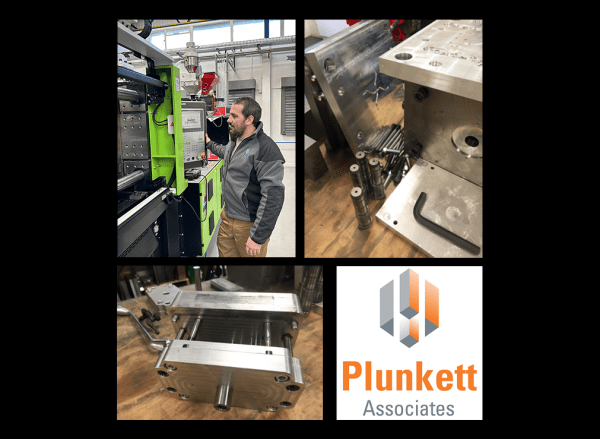
Bridge Tooling – What is it and When Should I Use it? | Blog
Bridge Tooling can also be known as development tooling or rapid tooling and defines a stage in development where there is a need for moulded parts, but production tooling is unavailable. Its name comes from the fact that it forms a bridge between prototyping and production.
When is bridge tooling used?
The requirement can be driven by several issues, for example:
- The production intent material is a ‘must have’ for evaluation purposes
- The quantity of parts required makes prototyping uneconomic
- A trial batch is required ahead of production release
- The design is not sufficiently stable to allow production tooling
- Initial part call-off is too low to warrant production tooling manufacture
Bridging the Gap
The process can also be used to ‘bridge the gap’ with motive originating from time saved, early availability of parts or cash flow. Often, the quantities are far from certain on new projects, making justification of tooling spend difficult.
Bridge tooling allows that ‘toe in the water, usually as a single cavity, that enables the production to tool spend to be deferred, and the market evaluated.
Aluminium, as opposed to steel
Aluminium is frequently used for bridge tooling as it permits faster machining, offers excellent thermal conductivity and can be worked/handled easily. Combined with standard mould frames and loose inserts, this helps to get a mould into a moulding press faster.
A result is a mould tool that costs less than a production tool, can be up and running in two to three weeks, and can produce from ten to a few thousand parts.
Whilst the individual unit cost may be higher than complete production parts, batches of hundreds of features may be completed faster than if conventional production tooling was used for the same quantity.
An ideal solution for smaller quantities of production parts
The standardisation of the process allows this tooling to be available at a price point that makes it a perfect solution when smaller amounts of production parts are required.
The advantages of injection moulding go beyond just the material options available; the consistency of product quality is extremely high, and the appearance and feel of the product implies a high volume, high-value item.
The challenge has always been to bring these advantages to low volumes without making the economics unattractive. Bridge tooling gives this opportunity, and Plunkett Associates is injection moulding from quantities as low as 50 parts.
Selecting the right process
Whether bridge tooling is an option for you will depend on quantities, part complexity and time available.
We can help assess your requirements and look at the unit costs. If you require a minimal production quantity, reproduction-readyd be worth talking to us today about bridge tooling.
Read more from Plunkett Associates here.
Plunkett Associates
+44 (0)1452 386608
Website
Email