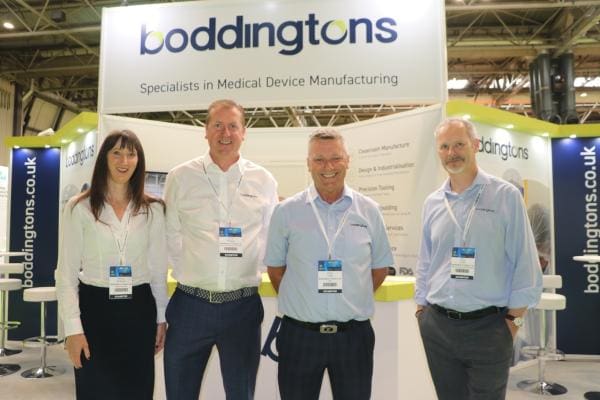
Medical Moulding – Putting it All Together at Boddingtons
Boddingtons Plastics is a four time winner of the UK’s Plastics Industry Awards (PIA) – Industrial Design category. Three of these Boddingtons PIA winners have been medical devices involving complex component and assembly work. The company’s exhibiting presence this year at both Medical Technology UK (Coventry) and Med-Tech Innovation (NEC Birmingham) has proven to be popular with OEMs and specifiers who are seeking manufacturing expertise in plastics technology. Chris Philpott, Boddingtons Business Development Manager outlines the factors involved and how manufacturing services at Boddingtons are helping drive the medical marketplace.
Covid 19 catalysed the industry
Although the Covid 19 situation may seemingly be calming down, the early stages of the pandemic revealed much about the world’s medical supply chains, the awareness of the design and manufacturing process and the state of healthcare supply generally.
Chris Philpott says that ‘Covid was not so much a wake up for medical devices but more like a spotlight on practices in the sector – some good, some bad.’
He notes that ‘large parts of public procurement had to get themselves educated very quickly indeed – realising, for example, that most medical components and assemblies are custom made to order – not simply waiting to be ordered from a catalogue and off warehouse shelves.
Even the simplest medical product needs to be designed and made fit for purpose at optimum cost and volume. Even in pandemics a visor or a face shield still needs strigent controls and thorough process validations including regulatory registrations via BSI, MHRA, FDA, and other relevant bodies.’
Marden-based Boddingtons was involved in a number of Covid device projects from the outset, including the company’s role in contributing to the UK’s ventilator manufacturing effort: At its peak, Boddingtons was manufacturing seamlessly for 24 hours a day for this project in order to satisfy demand.
The emergency project came about due to the high volumes required but with exceptional turnaround via a tool transfer request from the OEM responsible and teamed Boddingtons with other OEM participants.
Despite the extreme nature of the emergency, the nature of the medical industry – with its processing regime of new product introductions – allowed no corners to be cut for ventilator production. Suppliers simply had to work harder & faster.
Would-be suppliers needed to demonstrate capability, capacity and ideally the ISO 13485 medical manufacturing standard as a minimum condition of business together with Class 7 Cleanroom capability where needed. In addition, suppliers needed to show total project management & technical support – from first designs to full tool production, injection moulding volume manufacture, assembly, packaging, sterilisation potential and shipping.
All of these qualifications and more helped Boddingtons join the Ventilator Challenge in the UK. The moulding itself was a directly involved in the workings of the ventilator air tunnel. The OEM client specified all the features needed, including materials specification and colour from a TPX polymer blend from Mitsui.
A number of project tasks presented themselves from the outset; including tool transfer, repair and modification, preparation of production facilities and incoming materials; manufacture of gauges and purchase of fittings which featured in the product as part of the in process assembly.
Legal obligations and services at every stage
Chris Philpott notes that ‘even with all such expertise and resource at our disposal we were able to provide one further set of competences that typically help us to grow our business and support on numerous customer projects.’
The Boddingtons ‘extra mile’ involves the company taking full legal and administrative responsibility for the medical device components
This necessarily involves resources in staff, quality systems, legal know-how and experience of these issues in the medical market place. Boddingtons has calculated that the extra mile is well worth the effort.
‘Our services here are as much to protect the client as ourselves,’ says Philpott. ‘We operate a gated product introduction process in everything we do, and this breaks down the design, manufacturing and legal processes into clear and discrete phases – each stage completed, paid for and approved before the next stage begins.’
Mandatory testing and inspection
At the end of this road, the outcome for Boddingtons clients is that the company moulds, assembles, tests, packages and sterilises all medical components and devices that leave the factory gate.
‘All components are manufactured under our Quality Management System (QMS) certified to ISO 13485:2016 MDSAP,’ says Philpott and we thereby provide full control and traceability for all raw materials, manufacturing and sterilisation processes.’
He adds that ‘as the manufacturer, it is also our legal responsibility to make sure that all product is packaged and protected before it leaves us for the customer. The cmprehensive validation processes demand full testing of the chosen specification that will go into the market place. We have to continually monitor the performance of medical device packaging – for example sealed pouches for actual seal strength to make sure they maintain integrity and meet the initial validation and product specification.’
The sterility of injection moulded products within medical devices and the protection of the sterile barrier is key. Chris says that ‘a whole host of pull tests, die penetration tests – including visual inspection – are performed throughout the process.’
This also requires components and assemblies to be clearly labelled and identified – and here lot traceability is key. In-process product testing is also performed at Boddingtons. ‘This,’ says Chris ‘involves the checking of the performance of products through failsafe design of equipment – pressure testing products, for example, for the integrity and strength of the original design, and making sure that there are zero defects before being packaged for the customer.
Boddingtons also performs random destruction tests on products in order to check for build quality and performance.
Reshoring and tool transfer
This ‘belt and braces’ approach to client management means that Boddingtons is often approached by OEMs when their management of suppliers has become too distant, or when quality issues have deteriorated to unacceptable levels.’
‘These component projects are not necessarily too complex,’ says Chris, ‘but they often reflect a breakdown of priorities between moulder and customer.’ Some may simply involve optimising the volume and quality for a single high-volume component. Some may also involve reshoring mouldings from the Far East simply in order to improve lead times, project management and product quality.
Such tooling and moulding transfers regularly involve a complete re-examination of what may have been considered best business and industrial practice some years prior. Since then the tooling may have had many tens of thousands of hours in use and may need extensive repair, reconstruction or replacement. Grades of polymer may have developed and improved since the original component design – again, Boddingtons will review and recommend upgrades and changes when recommissioning production of the new component.
Continual shop floor and clean room reorganisation
In many ways Boddingtons is the antithesis of a typical contract injection moulder.
Chris says that ‘we can – and do – operate high-volume, fixed capital production year in year out but our approach to innovation and to new business means that we are continually re-inventing our shop floor in line with our new projects – re-siting or purchasing moulding machines for component production and also providing project-specific production, automation, clean rooms and assembly cells to the specifics needed for the new device‘.
Assembly cells at Boddingtons might include automation, welding, hand assembly, Hi-Resolution supported Camera QA inspections; packaging and printing services before despatch.
And then this line might be relocated, disassembled and/or modified in order to accommodate further med-tech business or a changing order.
Five years ago, Boddingtons was able – in addition to its main factory – to open a second class-leading purpose built £4.6m facility, including a modular Class 7 cleanroom capable of making Class 1 and Class 2 medical devices. The facility has more than doubled in size since – taking total investment to well over £6.0m.
‘Clearly we have a very competitive advantage in having very little issues to do with available factory space or available shop floor footprint,’ says Chris.
This is particularly so with issues of assembly which – for various reasons – can be very space intensive. Boddingtons most recent award winning project – a cancer detection unit – was such a case.
Boddingtons created a total of twelve injection moulding tools; some of these more than single cavity, comprising a grand total of 38 moulded parts in coloured, opaque and clear polymers that needed assembly at Boddingtons.
‘The assembly was complex,’ says Chris ‘and it included needle handling for which Health and Safety training and provision needed to be provided. We also created dedicated assembly workstations involving welding, automated gluing, a UV curing process whilst incorporating pressure decay detection.’
Polymers such as PP, HDPE and TPE’s – all medical grade materials – were developed into the device and tested by Boddingtons in preparation for the production manufacture.
‘At no stage’, says Chris, ‘did we feel hampered in terms of production resource or production space. Several manufacturing aspects – sharps inclusion and handling; automated UV curing and others – were completely new to us Boddingtons.
However, our experience in design-for-medical-manufacture had prepared us from the outset in the project management of the product and to handle all matters in house, maintaining control and continuity in approach to manufacturing this innovation & break through device.’
The next exhibition stop for the Boddingtons Marketing team will be Medical Technology Ireland, (September 21-22 Galway), followed by the prestigious Medica Compamed show in Düsseldorf, Germany, November 14-17th.
Read more news from Boddingtons here.
Boddingtons
+44 (0)1622 833700
Website
Email