
PlastikCity on Tour – Broadway
For June’s edition of PlastikCity on Tour, we headed East to Suffolk to visit James Rous, Chris Bird and Stephen Rayner of Broadway. A family-owned and independent company, Broadway is one of the country’s leading manufacturers of masterbatches, compounds and roto powders, supplying customers in the UK, Europe and beyond.
[Pictured above left to right – Will Clarke, James Rous, Chris Bird, Stephen Rayner, Carl Futcher.]
The Colourful Journey So Far
Established in 1997 by founder Joe Maynard and two other staff members, Broadway is a company that has enjoyed incredible growth over the past twenty-six years. Initially a specialist in custom colour masterbatches for the cosmetics and personal care industries, the company has grown vastly in size, reputation, production capacity and product offering from its base in the Suffolk countryside.
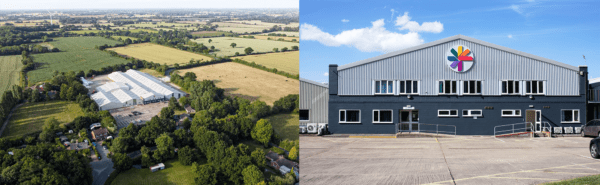
As demand for its masterbatches grew, so did the company, which has continued to invest in machinery and has steadily increased its production capacity ever since. In 2014, Broadway moved to its current 90,000ft2 site in Holton, further increasing capacity and enabling the company to bring all production and business activities under one roof.
Broadway continued to grow during and after the Covid pandemic – in 2021, they established Broadway GmbH in Germany whilst investing further in their UK site. Capacity was increased with a new production line and improved mixing facility. A new R&D and colouring laboratory was built in 2022, facilitating the development of new ideas, colourants and additive masterbatches. A new QC lab followed, aiding efficiency in implementing rigorous quality control procedures.
Twenty-five years in business was celebrated in May 2022, coinciding with the launch of a new company website and a rebrand from Broadway Colours to Broadway, to reflect its current offering being so much more than colour.
Today, Broadway is recognised as one of the UK’s leading suppliers of colour, additive and effect masterbatches, compounds and roto powders, employing around 60 staff, mainly from its Suffolk site.
The 50,000+ Colours of the Rainbow
It was at the company’s Suffolk HQ that we met with James Rous, Marketing Manager, Chris Bird, Sales Manager, and Stephen Rayner, Technical Manager, for a tour of the impressive site and to discuss the company’s history, current focuses, and some fascinating and innovative projects in the pipeline.
A significant advantage of having all operations on one site is that visitors can get an incredibly detailed overview of Broadway’s start-to-end process in one visit. While fantastic for our educational trip, the advantages for potential clients and brands working with Broadway are also evident. With visibility and control over all aspects of its processes, from specification and matching to production and dispatching, Broadway can offer a hugely customisable product range with short lead times.
Broadway works directly with moulders, designers and brands, and their on-site colour suite means multiple colour matches can be approved in one visit. When brand colours are paramount, colour masterbatches and compounds must be colour-matched perfectly in the first instance, and that consistency must be maintained batch-to-batch for the years to come.
Assisted by an impressive suite of QC equipment, including accelerated weather testing and spectrophotometers, the Broadway team must consider a number of criteria for each new formulation. Polymer compatibility, cost-efficiency, heat stability, lightfastness (fading or discolouration over time), toxicity and metamerism (colours changing appearance in different lighting conditions) must all be factored in when specifying new masterbatches and compounds.
One aspect I found particularly intriguing was the importance of metamerism, how certain colours appear differently in different light sources. It was something I had never considered as an outsider but was vital in Broadway’s processes and to ensure finished products appear on-brand and consistent.
Using a light cabinet to recreate different lighting conditions, Chris gave us a fascinating demonstration of how colour plaques appearing very similar in natural daylight (D65) can look vastly different under warmer ‘shop lighting’ (TL83), so the end use and location of every plastic product must be carefully considered. I recommend that anyone looking to learn more about this phenomenon click here to read a recent post from Broadway with an excellent video explanation of metamerism in action. I promise you’ll be surprised by the results!
Broadway’s colour matching is a free service, including formulating the colour match, posting colour plaques to the customer for approval, and (depending on the requirements) including a masterbatch sample for moulding trials if required. Any interested parties should contact Broadway directly through the company website for more information.
During the site tour, it became clear that the skill and experience of Broadway’s colourists are essential to the smooth running of its colour suite. From someone who couldn’t tell you the difference between taupe, tan or beige, watching these experts at work was very impressive.
Choosing from around 35 base pigments and dyes (above, left), staff such as Mark Turner, Broadway’s Senior Colourist (above, right), create unique formulations by weighing and adding constituents in different combinations and concentrations. I’m told that by combining technology, experience and instinct, the team can usually get very close to the target colour on the first attempt, in a process that is as much an art as a science!
From there, colour plaques are moulded and analysed, and any final tweaks are made to the formulation before the colour is remoulded and sent to the customer for approval. Once a colour is approved and an order is placed, the masterbatch or compound can go into production. Every production batch is checked against the retained master standard to ensure colour consistency.
Broadway recently celebrated its 50,000th colour match, a testament to the experience and history inside the company and to dedicated staff like Mark, who has been with the company since its foundation in 1997. Mark’s rare knowledge has been essential in training other staff members, as no formal training qualifications currently exist to hone a colourist’s skillset.
Green is the Colour
Sustainability is a topic of increasing importance on every company’s agenda, especially in the plastics sector, and it’s no different at Broadway.
The company demonstrates impressive environmental credentials, including ISO 14001 certification and achieving Silver EcoVadis Sustainability Ratings in 2022 and 2023. In 2023 Broadway installed 1,764 solar panels across its factory roof to create its own green energy used directly in the production of its materials.
As well as reducing the impact of its own operations, the products and services offered by Broadway further support its customers in achieving their own sustainability goals.
With the world focusing on reducing plastic waste, manufacturers are seeking more sustainable alternatives to virgin polymers, including the increased use of PCR (post-consumer recycled plastic). By incorporating a percentage of PCR into products sourced from waste packaging and end-of-life plastic, the footprint of plastic products can be significantly reduced. However, these materials can present their own processing and colouring challenges.
Fortunately, the Broadway team are well versed in colouring PCR, working closely with its customers to deliver dozens of matches for use in recycled plastics every week, and with the ability to manufacture compounds including up to 100% PCR, can contribute to the circular economy of plastics.
Black is Back
Another significant development for the sector is NIR (near-infrared) detectable black masterbatches. Traditionally, black plastic products utilised the ‘carbon black’ pigment to achieve a deep black colouration, but these products present inherent difficulties to NIR detection systems used at recycling plants. As explained in the diagram below, non-NIR black products absorb signals from the detector used at the waste plant, preventing its identification and therefore sorting and recycling.
Thanks to the clever chemistry of Broadway’s technical department, Broadway’s NIR-detectable masterbatches, compatible with both PET and PP, produce a high-quality gloss ‘piano’ black finish whilst meeting standard food contact regulations and safeguarding the ability to sort the end component in standard recycling waste streams, reducing waste to landfill.
After the tour and demonstrations concluded, we sat down with James, Chris and Stephen to discover the key to the company’s success.
To kick things off, what are Broadway’s key products and services?
James: “We supply three main product types: masterbatches, compounds and rotational moulding powers. Most orders are for custom colour-matched material, of which we recently hit the milestone of 50,000 matches. Our entire colour-matching process is incredibly detailed but efficient and is driven by our team’s technical knowledge and innovation.
“We also offer 122 ‘off-the-shelf’ colours in our ‘Universal Masterbatch’ range for those needing a colour quickly or when an exact colour specification isn’t required. Next-day deliveries across the UK are often achievable.”
Chris: “Our materials are used across all common plastics manufacturing processes. We supply masterbatches and compounds for use in injection moulding, blow moulding, ISBM (injection stretch blow moulding), film and sheet extrusion and 3D printing, as well as custom powders for rotational moulding.”
What is your target market? How has this evolved over time?
Chris: “Historically, our primary market has been in personal care products and food packaging, and we work directly with many household brands, including Boots, SC Johnson, Unilever and Reckitt, to name a few. We enjoy a strong reputation in this sector but also work in other sectors, with customers in construction, medical, toy manufacturing, pet care, electronics and many more.”
James: “We don’t just work with large brands either – we love to work with new businesses and SMEs, working closely by offering expert advice and guiding them on colour, effects and material choices to maximise the impact and functionality of their products. With customised masterbatch and compounds available for all plastics manufacturing processes, we serve a broad and flexible market and value every order, big or small.
“Sales of our custom compounds are increasing. Compounds are useful if a moulder doesn’t have the capability to dose masterbatch accurately or would prefer to pass the responsibility for colour dosing and distribution over to us. With the addition of more production lines, we’re able to be incredibly flexible, offering small minimum order quantities up to full truckloads of customised material.”
Chris: “Since 2011, we’ve offered rotational moulding powders, and we’ve just produced our 1,000th custom colour roto formulation. We also offer a stocked roto range of over 20 standard colours, including mottle effects for millstone, sandstone and marble. We have grades specific for kayak and canoe manufacturing, as well as tank grades, flame retardants, foams and antimicrobials, again with all specifying, manufacturing and QC happening in-house.”
Stephen: “Recently, we’ve been seeing increases in requests to colour PCR (post-consumer recycled plastic), especially since the plastics packaging tax was introduced in 2022, applying additional taxes to any plastic packaging containing less than 30% PCR content. Fortunately, we’ve been working with PCR for many years, so we have been able to support our customers with advice and guidance and clearly outline the limitations to consider.”
What are the limitations around colouring PCR?
Stephen: “It can be a slightly more complex process, and some compromises may need to be made in the target colour. Typically, PCR is tinted, so bright or translucent colours aren’t always achievable. The other challenge is that recycled polymer varies from batch to batch, so we need to adjust our formulas to create consistency between batches.
“However, brands and consumers should be increasingly accepting of compromises on aesthetics to increase sustainability, and we can demonstrate this entire process and limitations in our colour suite directly with our customers.
“We encourage all our customers to consider using PCR in their products, and anyone looking to learn about the colouring of PCR should get in touch to learn more. We can support you through the entire process.”
The launch of a European subsidiary is a big step. Was this in response to Brexit?
James: “Broadway GmbH was many years in the planning and expansion into Europe was part of the natural growth as a company before Brexit was confirmed. However, in a post-Brexit world, having a European base offers us some advantages and allows us to continue trading efficiently with our customers in mainland Europe.”
Chris: “Launched in Germany in 2021, Broadway GmbH enables us to better service the European market, with up to 25% of our sales exported outside the UK. We’ve found we can be competitive with European masterbatch suppliers on price and lead time.”
With over 25 years in the market, what has been key to Broadway’s success? What do you think sets you apart from the competition?
James: “Despite the company’s growth over the years, we retain our family values and customer focus. We work very closely with all our customers, big and small, and offer the highest level of service possible, using our expertise to deliver the right solution for every order.”
Chris: “I’d say our team’s experience and technical expertise are one of our main strengths. From our MD to sales, technical and production, we have staff in every department with over 20 years of experience in masterbatch. So, we have a deep knowledge of our sector and work closely with customers to overcome any specific challenges with bespoke solutions.”
Stephen: “Our production is set up specifically to maximise flexibility and agility. No single product is limited to a specific production line. This flexibility allows efficient production planning, resulting in short lead times – typically within five days from order. This also lets us economically serve smaller lots, enabling a very low minimum order quantity of just 5kg for custom masterbatches.”
Stephen: “Finally, I’d touch on quality – we’re proud to manufacture premium-quality products using the best quality pigments and raw materials available. Our on-site QC lab, testing facilities, stringent quality processes, and regulatory standards reassure our customers that they’re working with the highest-quality and compliant materials available on the market.“
What does the company have planned for the future?
Chris: “We are continuing to invest in our site, a new compounding line is due to be installed this summer to increase our capacity further. We’re also adding a new suite of testing equipment to enhance our QC processes, enabling more stringent mechanical and fire retardancy testing to be carried out on-site.”
Stephen: “We also have a few new notable products in the pipeline, which we’re excited to share with the industry.
“First is our new endothermic blowing agent masterbatch. A blowing agent creates a foaming effect during the production process, allowing small air pockets to form in the end component, leading to weight and density reductions. It can also improve the end product’s strength and thermal properties and reduce cycle times.
“Most blowing agent masterbatches on the market are exothermic (gives out heat) rather than endothermic (takes in heat). Our product leads to a more environmentally friendly and less hazardous process for the manufacturer.
“Developed and manufactured entirely in-house, this groundbreaking masterbatch has achieved weight reductions of over 8% in end components at just a 1% addition rate. This results in cost savings for manufacturers due to a reduction in the amount of polymer used, with lightweighting offering significant benefits in sectors such as automotive, aerospace and construction.”
James: “We’ve also recently launched a new odour-neutralising masterbatch, designed for use with recycled material. Instead of masking smells which can occur in PCR materials, the masterbatch physically traps smelly molecules in its 3D structure, removing odour from final products. After months of research from our R&D scientists, we’ve been conducting trials with UBQ Materials, an innovative material solution which includes all sorts of waste from landfill. We’ve had very encouraging results in both colouring and odour elimination.”
Stephen: “In terms of staff development, we’re working alongside colleges and universities to develop a bespoke training programme for colourists. No such training programme currently exists in the UK, and we see it as essential for ourselves and the wider industry to provide training and development in this unique role for the years to come.
“I’m developing a 2 to 3-year training programme, which will give a level 4 or level 5 qualification on completion from a college or university (equivalent to an HNC, HND, NVQ, apprenticeship or foundation degree). My personal career background leans heavily toward training and development, so I’m aiming for Broadway to become the UK’s ‘Centre of Excellence’ for colour training. Our facilities and expert knowledge will support this programme.”
Chris: “For future developments, we’ve started some exciting research into bio-based pigments. By using UK-made bio pigments, we hope to offer materials using carbon-neutral or even carbon-negative colourants. This work is ongoing, and there’s much to consider, so stay tuned for more information on this in the future!”
Is Broadway attending any exhibitions or other events this year?
James: “Yes, we’ll be at Interplas at the NEC Birmingham in September with our biggest and best stand ever! Please visit us on stand B12 to discuss our latest developments.”
Finally, do you have an official or unofficial company philosophy or mantra?
James: “We really are so much more than colour. Creating custom colours for plastics will remain a fundamental part of our offering, but it’s important that the breadth of our products and quality of service is understood across our industry.
“Our technical team are doing some fantastic work. It’s great to see positive results from external trials on additive masterbatches developed in-house, such as our endothermic blowing agent. We have a market-oriented approach to product development as well as a team which understands customer requirements and works diligently to deliver against these.
“The ‘Broadway Values’ are proudly displayed in our reception for our customers to see, and they summarise our company identity perfectly.
“The values are:
- Quality
- Expertise
- Adaptable
- Responsible
- Trustworthy”
Thank you to James, Chris and Stephen for taking time out of their day to show us around every corner of Broadway’s impressive facility, and to educate us on the fascinating and colourful world of masterbatch!
If you’d like to learn more about Broadway’s services, new products, or need assistance in colouring material with high PCR content, reach out to the team here, or catch Broadway at Interplas in September.
After a very enjoyable and informative visit, we highly recommend booking a trip for yourself!
Look out for the next edition of ‘PlastikCity on Tour’ to learn more about our excellent UK-based partners.
There are now well over 260 active partners represented on the PlastikCity site, many of which offer highly specialised products or services to our sector.
During our everyday course of business, we’ll be making a point of visiting as many of these partners as we can and using the time to better understand what they offer the market. We’ll then showcase them through this ongoing series of articles.
Maybe you can benefit from their services!
Read more news from Broadway here.
Broadway
+44(0)1986 875 100
Website
Email