
Sustainability in UK Automotive Event a Cross-Sector Success
Hosted by ENGEL UK, JLR, Plastribution and Summit Systems on 28-29th November in Warwick, the “Driving Mobility – Sustainably!” event attracted dozens of plastics professionals from a variety of sectors. Attendees were treated to a day of insights into the current and future trends, requirements and sustainability initiatives of the UK automotive industry from leading industry players.
The automotive industry in the UK and Ireland has long been maligned and underestimated, navigating its fair share of challenges in recent years, including Brexit, supply chain issues and component shortages, to name a few. However, in recent months, the winds of change have started to blow a refreshing breeze, as the automotive landscape in the UK is finally showing signs of optimism and renewal.
Held at ENGEL UK’s HQ in Warwick, the recent “Driving Mobility – Sustainably!” event sought to explore the reasons behind this optimism, and to lay out the upcoming opportunities for companies working in this sector. In particular, the rise of electric (EV) and hybrid (HEV) vehicles as the perceived way forward for the sustainable automobiles of the future has led to new opportunities for UK manufacturers, as the industry continues to shift away from traditional ICE (internal combustion engine) vehicles, and towards EV and HEV production.
In typical understated British fashion, we’re urged to not get ahead of ourselves, as the road to recovery may be long and littered with unknown speed bumps. However, with the disruption that EV production is adding to the manufacturing landscape and an ongoing focus on sustainability within the industry, many new and changing opportunities have opened to UK-based manufacturers.
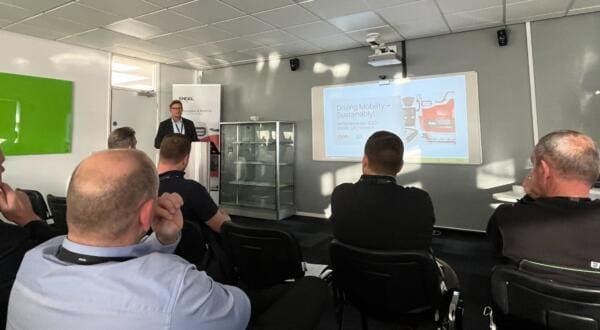
As mentioned at the event by WHS Plastics CEO, Paul Nicholson in his talk titled “Status Quo of the Automotive Industry Today,” significant funding for EV and battery-related projects has recently been confirmed across the UK, with Stellantis (Vauxhall) committing over £100M at its Ellesmere Port site, Nissan committing a further £2B to its Washington facility and Jaguar Land Rover planning to invest £15B in the next 5 years at its Halewood plant in Merseyside, with more positive news from Tata Motors, Enivision and others in recent months. We may not be looking at the roaring auto industry of days gone by, but signs of change are beginning to be recognised, for the optimists among us at least.
The event also highlighted that our homegrown automotive industry is something to be proud of. A vital sector of the UK economy and key to advancing toward net zero, automotive-related manufacturing contributes £67B yearly turnover to the UK economy, with 182,000 people employed directly in manufacturing and over 750,000 employed in the wider sector. Despite concerns over trade barriers and exporting since 2016, encouragingly around 80% of vehicles manufactured in the UK are exported, to 130 different worldwide markets. (Stats courtesy of SMMT).
Clemens Kastner, ENGEL’s Head of Business Development for Automotive and Mobility added some context to these changing markets, highlighting growing opportunities for plastic component manufacturers specifically. The obvious trend with the move to EVs, or ‘smarter’ vehicles is the battery components and housing, but opportunities extend further than this, into some components you might not have considered.
A growing trend in modern vehicle design is the inclusion of ‘smart panels’ on a car’s exterior, as shown on the exampke below. These large body panels are manufactured in multiple layers, often of different materials, each containing a variety of technology now coming as standard in high-tech, modern vehicles. An array of sensors, lighting and cameras and associated electronics need to be incorporated into the assembly, along with functional and decorative films, all while requiring very high shot-weight machinery. A complex component, but a strong example of the changing requirements in vehicles, and the increasing value that plastic and plastic composite materials can provide in terms of flexibility, lightweighting and aesthetics.
Further challenges for manufacturers working in this area is the potential requirements for moulding of large products, such as battery housings. Clemens walked attendees through a variety of fascinating real-world examples of these products, and the resulting manufacturing solutions, with ENGEL supporting its customers with large tonnage machinery solutions to support this growth (including a particularly impressive ENGEL duo with 8000T (!) clamping force, as an extreme example!).
Jaguar Land Rover’s Nicola Keers and Nat Spencer delivered a series of presentations with a particular focus on the legislation and sustainability initiatives driving these market trends, and the pressures (and opportunities) this creates.
This provided a fascinating insight into a market leader’s Net Zero journey and the landscape for developing sustainable products, as the JLR team highlighted the EU directives driving this change, and how they have taken action to meet, and often exceed these targets, as they take a long-term approach to addressing such important issues.
As expected, the legislation can be muddy, complex and sometimes contradictory, but EU ELV Directives especially are driving change in OEMs, and therefore are now filtering down the automotive supply chain.
JLR’s Ian Ray then delivered a talk about the realities of using recycled materials, and how action must be taken to maintain the utmost quality throughout the vehicle supply chain. As manufacturers will be aware, working with recycled materials isn’t always straightforward, and with strict legislation soon coming into effect governing the manufacture, composition, disassembly and recycling of vehicles, these challenges become ever more important to address. The answer? Well, one huge part, according to Ian, is the implementation of ‘smart factories’ – using software, data and digitalisation to control, record, and optimise process parameters to create higher levels of consistency and quality, and importantly, traceability.
Other speakers at the event included Paul Edmonson of Maguire Europe who spoke about the equipment technology used by Maguire to support its customers in the sector. Paul highlighted the extremely efficient Maguire Ultra Dryers, which as well as being hugely energy-efficient, uses unique vacuum technology to increase drying speeds with a very low energy requirement, perfect for the rigors of automotive moulding.
Phil Little and Ian Chisnall of Plastribution gave us an overview of the huge variety of polymers used in car manufacturing, giving examples of sustainable alternatives useful in certain applications. Whether its Bio-based, Bio-circular or recycled, the Plastribution technical team is well-placed to advise and source materials for customers in the automotive sector. Phil also showed attendees a selection of sustainability commitments from global brands in recent years, showing that the demand for high-quality recycled polymers will only increase as these goals are realised.
Finally, ENGEL’s Process Manager, Mark Edwards showed attendees how ENGEL is supporting its customers with its digital ‘smart factory’ products. The event ended with Mark giving live demonstrations of the ENGEL IQ weight clamp control and other industry 4.0 connectivity offering advantages to manufacturers. (Pictured above) As highlighted earlier in the day, the adoption and intelligent use of these i4 technologies is key to the future of the industry and ENGEL has a significant offering already in place to support this goal.
Overall, the event was a fascinating insight into the UK automotive industry, leaving attendees with a glimpse of promise that the sector will continue its recovery in 2024 and beyond. As for the future, for now we agree it is EVs and battery technology. With significant commitments from automakers with battery and EV sites already on UK soil, I hope the move to battery technology can be a catalyst for a revival in the sector and a boon for UK-based manufacturers.
To end, some positive stats courtesy of Richard Shepherd, who joined the event by video link to present AMI’s latest automotive industry update, further backing up the discussions throughout the day. Plastics Europe estimates that the average weight of plastic per vehicle will increase by 30% by 2050, the global automotive plastics market will reach $50B annual sales in 2024, and automotive-plastics demand is expected to increase by around 10% as a result. Let’s hope that this translates into more quality automotive products being produced in the UK and Ireland, for use at home, and worldwide!
Thank you to ENGEL, Plastribution and Summit Systems for hosting a well-organised and informative event, and for presenting their market-ready solutions for addressing the issues raised in the presentations. Also thank you to the speakers for sharing your expert knowledge and insights, on what was an inspirational event, personally filling me with pride and a newfound positivity for the future of the sector.
Read more news from ENGEL here.
ENGEL
+44 (0) 1926 335000
Website
Email