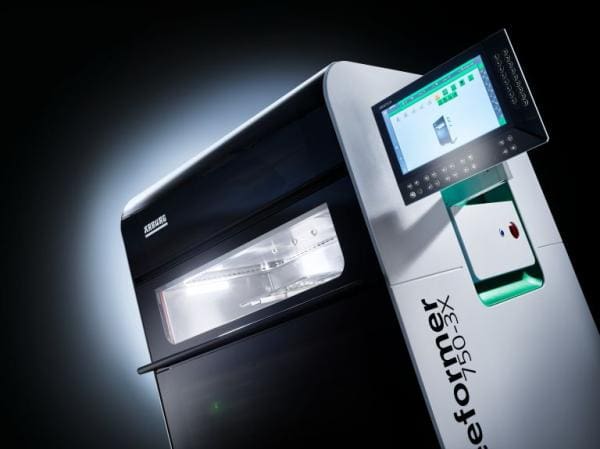
Huge freedom: New Freeformer with Extremely Large Build Chamber
Arburg’s new Freeformer 750-3X celebrated its world premiere at K 2022. The size of the build chamber is particularly impressive, as it is around 2.5 times larger than that of the Freeformer 300-3X – with the same external dimensions. The new machine is also faster due to its higher discharge frequency and more economical, as it can not only produce larger parts, but also several articles in one work cycle. Through the use of the Gestica control system, which has been optimised for the additive manufacturing process, the Freeformer 750-3X also delivers improvements in process stability, part quality, and build time optimisation.
The principle of material preparation in the Freeformer 750-3X remains the same as in the Freeformer 300-3X, but the entire system has been optimised to make the new machine more compact. Purely from the outside, the Freeformer 750-3X is therefore indistinguishable from the 300-3X, as it has the same external dimensions. However, the part carrier is around 2.5 times larger, now measuring some 750 square centimetres – which is also what the name of the new system refers to.
The significantly enlarged build chamber measuring 330 millimetres x 230 millimetres x 230 millimetres, in which, incidentally, temperatures are kept stable and constantly homogeneous, is the result of several technical innovations. These include more compact and slimmer melt pressure generators for dosing and injecting, which use servo motors from AMKmotion, a company in the Arburg family.
The entire system, comprising the preparation and discharge units, has been pressure-optimised and is therefore tailored to the conditions of additive manufacturing and Arburg Plastic Freeforming (APF). In the case of the adapted melt pressure generator, the focus is primarily on the precision and repetition accuracy of the melt discharge, which in turn serves to produce uniformly sized, constant droplets. Cost reductions are also achieved thanks to the hardware adaptations that have been implemented and that also allow the three discharge units to be made more compact and arranged closer together. Compared to the Freeformer 300-3X, their design is 100 millimetres “slimmer”.
Gestica control system as a common platform
The innovative Gestica control system familiar from the Allrounder injection moulding machines, with software appropriately adapted to the production process, is now also used as standard on all new Freeformers. This means that injection moulding and industrial additive manufacturing are on the same platform in terms of controller technology. The aim for the control system was a “push-button solution”, in other words, simplified operation that automates the start-up sequence, for example.
In addition, simultaneous dosing, which reduces build time, is also possible. Automatic calculation of the material required per layer helps to reduce the residence time in the process. Optimised data processing, for example in the areas of lattice structures and faster discharge, significantly reduces the costs per part. A higher discharge frequency is now also possible. As a result, process-optimised latticed support structures can be created, for example, with a build time that is up to 55 percent faster than with “conventionally” built structures.
The innovations in the area of control extend specifically to the “production control” sectors, with intuitive operation such as overviews of the job status and production, as well as the
“intelligent start-up sequence” for preparing production, which is processed completely independently. In addition, there is the demand-oriented, variable dosing, reduced material residence time in the cylinder, parallel dosing of individual sequences and hence reduced build time, and optimisation and expansion of data preparation with regard to the lattice structure build strategy and the break-away support (i.e. the facilitated removal of support structures). This all contributes to improvements in process stability, part quality and build time optimisation.
Build time reductions of up to 85 per cent
The “hollow tube” sample part clearly illustrates the advantages of the new Freeformer 750-3X. Previously, the standard printing time was 17 hours and 33 minutes. Optimising the lattice strategy (support structures), accelerating the droplet discharge, boosting the frequency and increasing the layer thickness from 0.2 millimetres to 0.25 millimetres without compromising quality has reduced the printing time to seven hours and four minutes. This means a final build time reduction of 60 percent.
Another interesting example is the additive manufacturing of an automotive window seal. The standard printing time was previously 67 hours and 32 minutes. Due to the enlarged build chamber, the parts can now be assembled horizontally instead of vertically. Added to this are a modified lattice strategy (support structures), accelerated droplet discharge, increased frequency and likewise thicker layers – again 0.25 instead of 0.2 millimetres – resulting in a total reduction in printing time to nine hours and 38 minutes. That means a reduction of 85 per cent!
Arburg is a trend setter
In industrial additive manufacturing, the trend is clearly moving in the direction of high cost-effectiveness in day-to-day production, both in the manufacture of larger individual parts and in the assembly of multiple articles in one work cycle. The Freeformer 750-3X meets precisely these challenges. This system closes the gap from pure prototyping to small series production, because not only has the size increased, but also the speed of construction. The handling has also been adapted to make it easier for users to operate the machine in their production environment. The feed hopper volumes have been doubled and accessibility in the area of the maintenance flap has been improved.
All this delivers even more individuality, functionality, increased user-friendliness, lower costs and freedom in part design, among other benefits, as well as an effective acceleration of output through the assembly of multiple parts in a single work cycle.
Read more news from ARBURG here.
Arburg
01926 457000
Website
Email