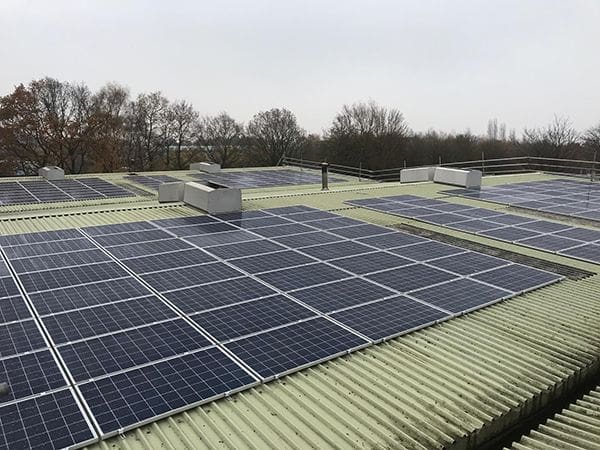
Life is ‘Greener’ at LVS
Telford based LVS Small Plastic Parts have been working hard to demonstrate how a modern injection moulding company can be environmentally conscious. This has involved both energy conservation and generation, as well as reducing the impact of material loss to the environment.
New Solar Panel Array
The company has recently completed the installation of a large array of roof mounted solar panels. The project was supported by Optimise Energy UK Ltd, who previously helped LVS secure grants for LED lighting, Power Factor Correction and a more efficient compressed air system.
The 90kW Solar PV array consists of 345 panels with the ability to generate 80,730 kWh of electricity per annum. This equates to reduced emissions of 45.20 tonnes of CO2 per year, or 20.8 acres of forest being saved.
Energy Efficient Production Equipment
Melting and injecting plastic at high temperatures and pressures requires a lot of energy, Moulding machines manufactured in the 1990s typically using one whole kilowatt of power to process just a kilo of raw material!
LVS have tackled this issue by investing in the latest injection moulding equipment. Their most recent acquisition was a 500-tonne NEGRI BOSSI CANBIO sT machine. State-of-the-art servo pump technology delivers the exact amount of energy required for each phase of a production cycle. For example, the machine currently produces an electric shower back plate with a 75 second cycle time. During the 45 second ‘cooling time’, the machine is in an idle state.
Ethical Processors Assessment
LVS have worked closely with PlastikCity to develop a new standard for plastic processing companies. The ‘Ethical Processors’ evaluation is designed to ensure that companies are minimising the risk of plastic pellets entering the environment, primarily through good housekeeping practices.
The assessment also focusses on reducing ‘waste to landfill’ and control of scrap production levels. Scrap mouldings are inevitable, especially during the machine ‘start-up’ stage. As part of the audit, LVS had to demonstrate that different polymer types were segregated and correctly packaged. This then allows a third-party recycling specialist to produce a recycled grade that is optimised for reuse.
Forward planning for future recyclability is also encouraged during the design phase of new products, as well as consideration for the use of recycled grades and returnable packaging.
When asked about the company’s approach to environmental issues, Managing Director, Simon Anderson commented,
“We do not manufacture any ‘single-use’ plastic items at LVS, but still believe that we should demonstrate an ethical approach to any activities that can directly or indirectly impact on the environment.”
“Our sector has recently received a lot of bad press when the reality is that many plastic items can have a positive impact on the environment. For example, we produce a lot of automotive interior trim items that have directly replaced much heavier metal components. Lighter vehicles use less fuel or have extended ranges, the latter being critical for electrically powered vehicles.”
LVS Small Plastic Parts operate 36 modern injection moulding machines, from 22 to 800 tonnes locking force, including a 450-tonne twin-shot model. Larger machines also have dedicated full-servo cartesian robots. All machines are supported by the latest and most energy efficient ancillary equipment, further reinforcing the company’s commitment to minimising their Carbon Footprint.
LVS Small Plastic Parts
01952 290 666
Website
Email