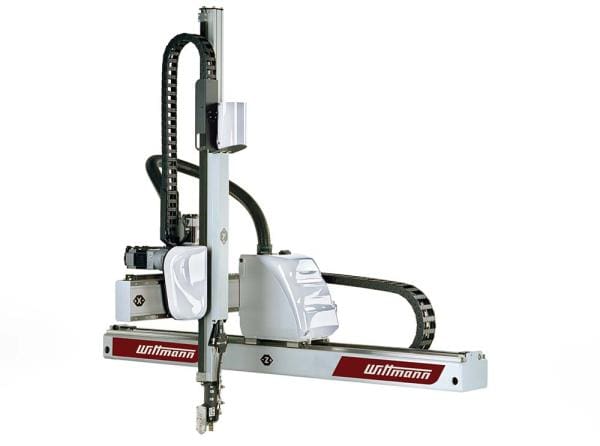
Wittmann Battenfeld UK to Present Automation Solutions at Plastics Live
Wittmann Battenfeld UK will present its robotic and automation solutions as part of its presence at the upcoming Plastics Live 2022 exhibition next month in Coventry, July 5-6.
The dates for this new UK show fall between last year’s Fakuma exhibition in Southern Germany and this Autumn’s world-leading triennial show for the global industry in Düsseldorf, Germany, October 19-26th.
Industry watchers therefore expect a batch of new Wittmann robotic innovations to be introduced in five months’ time. Meantime, however, Wittmann has much to share and re-emphasis in terms of its current and successful automation solutions for injection moulders.
The Wittmann Primus best-selling robot, for example, is the bedrock of Wittmann automation growth in recent years. This Primus is a solution that can be introduced most anywhere in the injection moulding cell and it can also work with any make of injection moulding machine.
The proof of its popularity and price-competitiveness is now evident in contract moulding shops throughout the UK and Ireland. In terms of robots Wittmann also supplies many ‘horses for courses’ and the Wittmann linear range – in terms of payload, design, end of arm tooling and sheer variety of design – is peerless among industry suppliers.
A leading reason for the breadth in the Wittmann portfolio is that, since its inception, the company – headquartered in Vienna Austria – has always set out to continually innovate for the industry: More often than not the injection moulding community demands increased performance within reduced production time. Wittmann accordingly pushes technical boundaries on behalf of its customers; innovating its robots in order to make life easier for the user – while also saving time and money.
Top quality build, ergonomic design and footprint and speed (allied to reduced cycle time) are therefore traditional qualities with the Wittmann name. Less publicised until recently has been the company’s insistence on low-energy production and continual reduction of energy requirements.
Global events and politics in 2022 have now made energy cost a critical issue for today’s injection moulders. Wittmann will therefore use the Plastics Live show to highlight its class-leading and low-energy equipment in all categories. So much so that Wittmann has this year launched a campaign to ‘Take the Wittmann Energy Challenge’ – an initiative currently being rolled out globally.
The continual development of Wittmann’s robots and automation solutions goes hand in glove with the development of the company’s people.
In the last decade, automation – and its close cousin Industry 4.0 – has increased in simplicity for the user/operator, while increasing in complexity for the designer, installer and service engineers.
The automation of injection moulding processes is therefore not an industry for ‘box shifters’ or DIY created solutions.
Instead the injection moulding community typically stands in need of an integrator of automation systems who can stand behind the equipment supplied and then best advise its optimum use in production.
Wittmann has been supplying this market for over 35 years and the experienced Wittmann team fulfils exactly this integrating role; helping the client to overcome typical issues and obstacles and tuning its manufacturing for the most effective outcomes.
In the initial stages a number of CAD generated blue prints and designs of the proposed production cell are typically generated by Wittmann until settled and agreed by the customer. The pieces of equipment are typically then road tested before delivery and commissioning at the customer’s factory.
The automated cell design includes all the necessary guarding and protection measures and also end-of-arm tooling needs. Risk assessment and method statements (RAMS) are completed before Wittmann engineers are dispatched to the customer factory and then the protocols of ISO 13857 are followed. If a Wittmann customer buys a company Insider package or a complete cell then all of these matters and documents are supplied as standard.
The Wittmann team also helps ensure customer compliance with all necessary risk assessments, CE markings and issues of health and safety.
Once commissioned it becomes clear that today’s Wittmann robot can not only be paired with any moulding machine but can also control production elements outside the press such as material feeds, temperature controllers and conveyors. In this way a Wittmann robot can be the gateway to a 4.0 style of production.
For reasons of running cost and efficiency it is now rare to find a new and unautomated injection moulding cell. And although Wittmann robotics generally take a secondary role behind the ordering of the primary injection moulding machine it is very clear that the technology is further increasing its role in manufacturing today.
Read more and register for Plastics Live here.
Read more about Wittmann Battenfeld UK here.
Wittmann
01933 275777
Website
Email